ISRO’s 3D-Printed Spacecraft 24
ISRO’s 3D-Printed Spacecraft
By successfully testing the PS4 engine—which has been redesigned for production using state-of-the-art additive manufacturing (AM) techniques, also known as 3D printing—for an extended period of time, the Indian Space Research Organisation (ISRO) has made a significant milestone. This ISRO’s 3D-Printed Spacecraft, also known as 3D-Printed’ Rocket Engine which displays scientific prowess and innovative spirit within the country, represents a significant advancement in India’s space exploration aspirations.
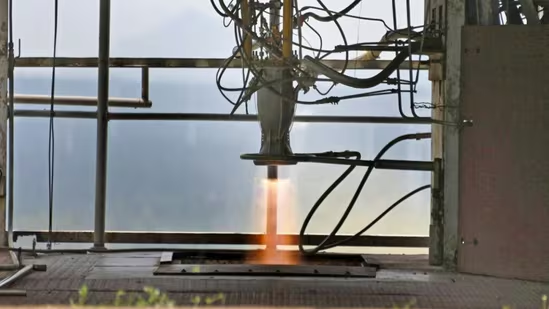
Rocket engine production has historically required a number of complex machining and welding operations that took a significant amount of time and raw materials. Still, ISRO has transformed this method with the use of additive manufacturing. Amazing efficiency advantages are shown by the ISRO 3D Printed Spacecraft, also known as the 3D-printed’ rocket engine, which is now built as a single component utilizing additive manufacturing technology.
The PS4 engine shows impressive efficiency increases, now that it is built as a single unit utilizing additive manufacturing technology. According to ISRO, this new manufacturing strategy saves a remarkable 60% on production time and 97 percent on raw material use. These developments improve the space program of ISRO’s agility while also making it more cost-effective.2
The liquid rocket engine made with AM technology underwent a successful 665-second hot test on May 9th, demonstrating the dependability and effectiveness of this novel approach. In order to reach bigger milestones in space exploration, it demonstrates ISRO’s dedication to pushing the boundaries of technology.
An essential part of the upper stage of the Polar Satellite Launch Vehicle (PSLV), the PS4 engine has been a mainstay of ISRO’s satellite deployment operations. This engine is essential for launching payloads into their intended orbits, with a vacuum thrust of 7.33 kN.
The PS4 engine’s adaptability is further demonstrated by its use in the PSLV’s Reaction Control System (RCS) of the first stage (PS1), underscoring its significance for the accomplishment of the mission.
Follow our Digiknowledge.co.in page for the latest updates about technology, bikes, cars, sports, lifestyle, and many more.
Earth-storable bipropellant combinations are used in the engine; in pressure-fed mode, monomethyl hydrazine is used as fuel and nitrogen tetroxide as the oxidizer.
This engine, created by the Liquid Propulsion Systems Centre (LPSC) of ISRO, is the result of years of research and development work focused at improving the effectiveness and dependability of propulsion systems for space missions.
India’s increasing proficiency in space technology is demonstrated by ISRO’s success in redesigning and producing the PS4 engine through the use of sophisticated additive manufacturing processes. It also serves as a reminder of India’s dedication to innovation and independence in the aerospace industry.
These developments are sure to have a significant impact on how India’s space program develops going forward and how it contributes to the international space community as ISRO keeps pushing the envelope of space exploration.
What is a 3D-printed rocket?
A major development in the production of spacecraft is the 3D-printed rocket. Metals, polymers, or composites can be used as raw materials to create layer by layer construction of the rocket’s structural pieces, engine, and fuel tanks using additive manufacturing processes.
When compared to conventional production techniques, the additive manufacturing process has various benefits. Engineers may now develop complicated geometries and optimize structures for efficiency and performance, giving them more design options.
What are the benefits of 3D-printed rocket?
- More efficiency and cost savings are possible with 3D printing since it may cut down on manufacturing time and material waste.
- The cargo capacity and overall performance of the rocket are further improved by the lightweight, strong structures made possible by 3D printing. Engineers can attain higher strength-to-weight ratios and more velocity or payload capacity for their rockets by optimizing the design and material qualities.
- The requirement to guarantee the dependability and caliber of printed components is one of the difficulties that come with 3D printing rockets, despite these benefits. In order to ensure that they can resist the harsh conditions of spaceflight, such as high temperatures, pressures, and vibrations, aerospace-grade materials must pass strict testing and meet strict performance standards.
- However, 3D-printed rockets have a lot of potential for the future of space travel as additive manufacturing technology develops. They open up new missions, prospects, and capabilities in the field of space travel by providing an economical, effective, and customized method to spacecraft construction.
What materials are used to make 3D-printed rockets?
Lightweight metal alloys including aluminum, titanium, copper, nickel, and chromium are fused together using additive manufacturing techniques to create 3D-printed rockets.
What are the safety precautions for 3D-printed rockets?
Chronic headaches, nausea, and irritation of the eyes, nose, and throat can result from 3D printing-related VOC exposure. ABS and PLA nanoparticles, which are created during printing processes, have the potential to penetrate deeply into lung tissue if inhaled.
What is the largest 3D-printed rocket engine?
The ISRO Liquid Propulsion Systems Centre (LPSC) created the PS4 engine, which runs on a bipropellant combination of monomethyl hydrazine as fuel and nitrogen tetroxide as the oxidizer. Wipro 3D, an industry partner in India, created the engine that was manufactured by additive manufacturing.
Which is India first 3D-printed rocket engine?
The world’s first single-piece 3D-printed engine is the Agnilet engine, patented by Agnikul. It was successfully test-fired in early 2021 after being fully designed and produced in India.
Pingback: Agnikul Cosmos: The first 3D-Printed Rocket Engine 24 - Digiknowledge
Thank you so much for your kind words and support! I’m delighted to hear that you find the website and posts helpful. If you have any questions, suggestions, or topics you’d like to see covered, please feel free to let me know. Best regards to you as well!
Pingback: Pushpak: ISRO's Reusable Launch Vehicle: 3rd Success
Thank you for your kind words! I’m glad you found the content valuable and appreciate the link on your website. If you have any specific topics you’d like me to cover or any feedback to improve the content, feel free to let me know. I’m here to help!